It’s smoother, more accurate, quieter, and doesn’t scare the children.
My previous scroll saw was an attachment for my treadle powered lathe. It was built from a postage stamp sized drawing by Roy Underhill. While it served well for years, it is a clanky, rickety, wobbly, insanely noisy collection of loose parts pretending to almost work as a saw. Accuracy is subjective. Yet, I cut many wood carving projects with it and was satisfied until arriving at a new project that wants several parts thicker than the saw could handle; basswood parts that are 3 inches thick.
This new saw, also treadle operated, is a simple frame saw that has the frame moving in a vertical plane, riding very smoothly on drawer slides.
The support frame is simply an unfinished flat assembly of construction grade 2 x 4 lumber, joined by half-laps. It clamps to the front face of my workbench. Drop a rope from the bottom of the moving frame, loop it around a hinged treadle, and we have the motive power that pulls against the spring at the top of the support frame. That spring is only a couple of strips of quarter inch thick lattice, and more rope. Functional, not pretty. It has the added benefit of storing away in minimal space.
For the table that supports the workpiece, I use my woodcarving bench-on-bench sitting behind the frame. Clamped to the bench is a piece of cabinet shelving with a hole drilled for the blade. Simple, and as with the other parts, easily stored in minimal space.
The saw frame itself is poplar, using bridle joinery. Most important are the blade holding pins and blade. These are parts from the Tools For Working Wood 12″ bow saw. I’ve used them before for a wonderful turning saw and for that earlier scroll saw. I cannot say enough good about them. The bottom pin has its flange trapped by a wood block screwed to the bottom of the frame. The top pin is adjustable thanks to being pinned inside a lamp pipe which can move inside that upper block. Tensioning is via a slightly bent cross bar. A variety of blades from TFWW offer a good range of cutting options.
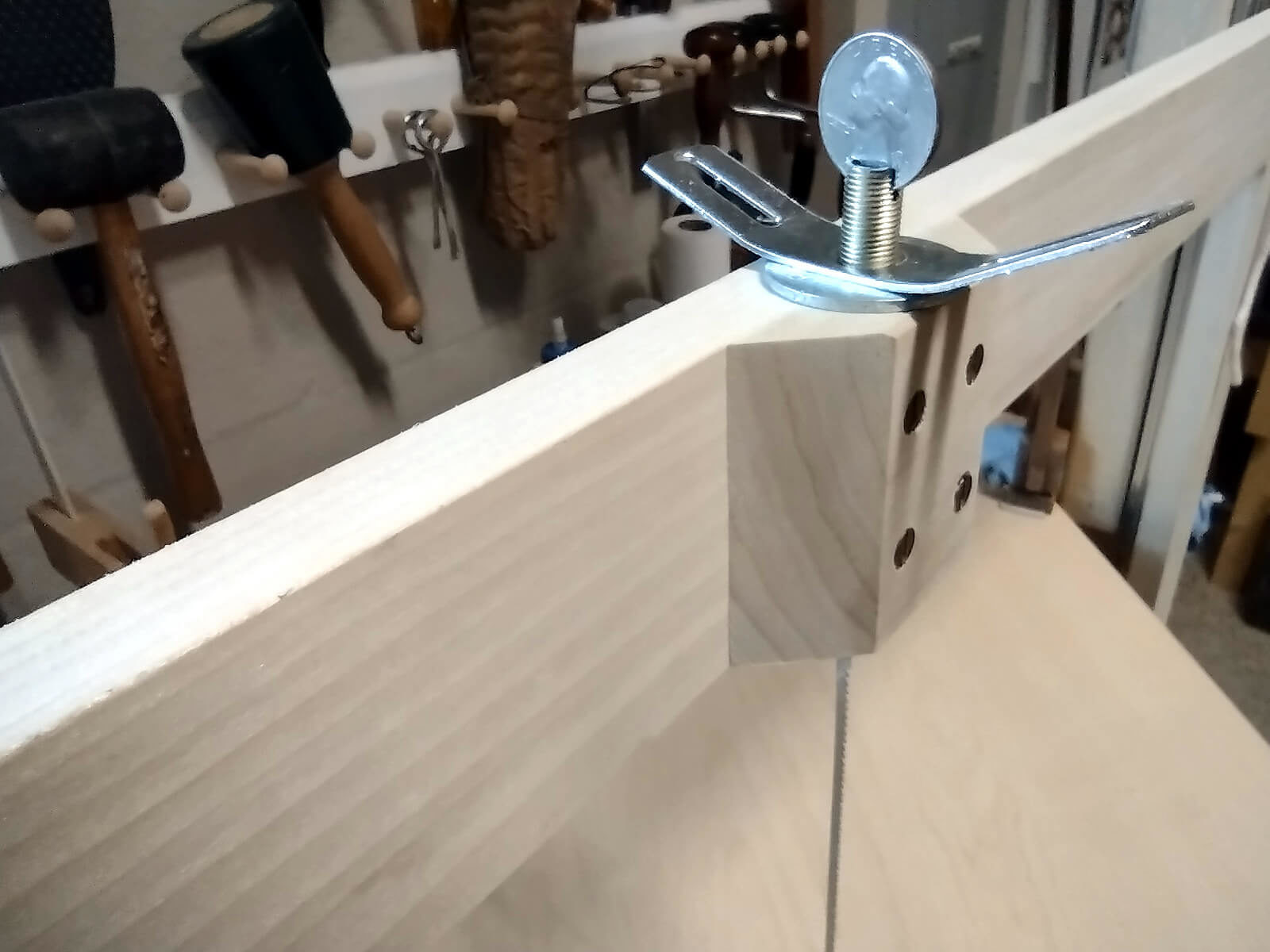
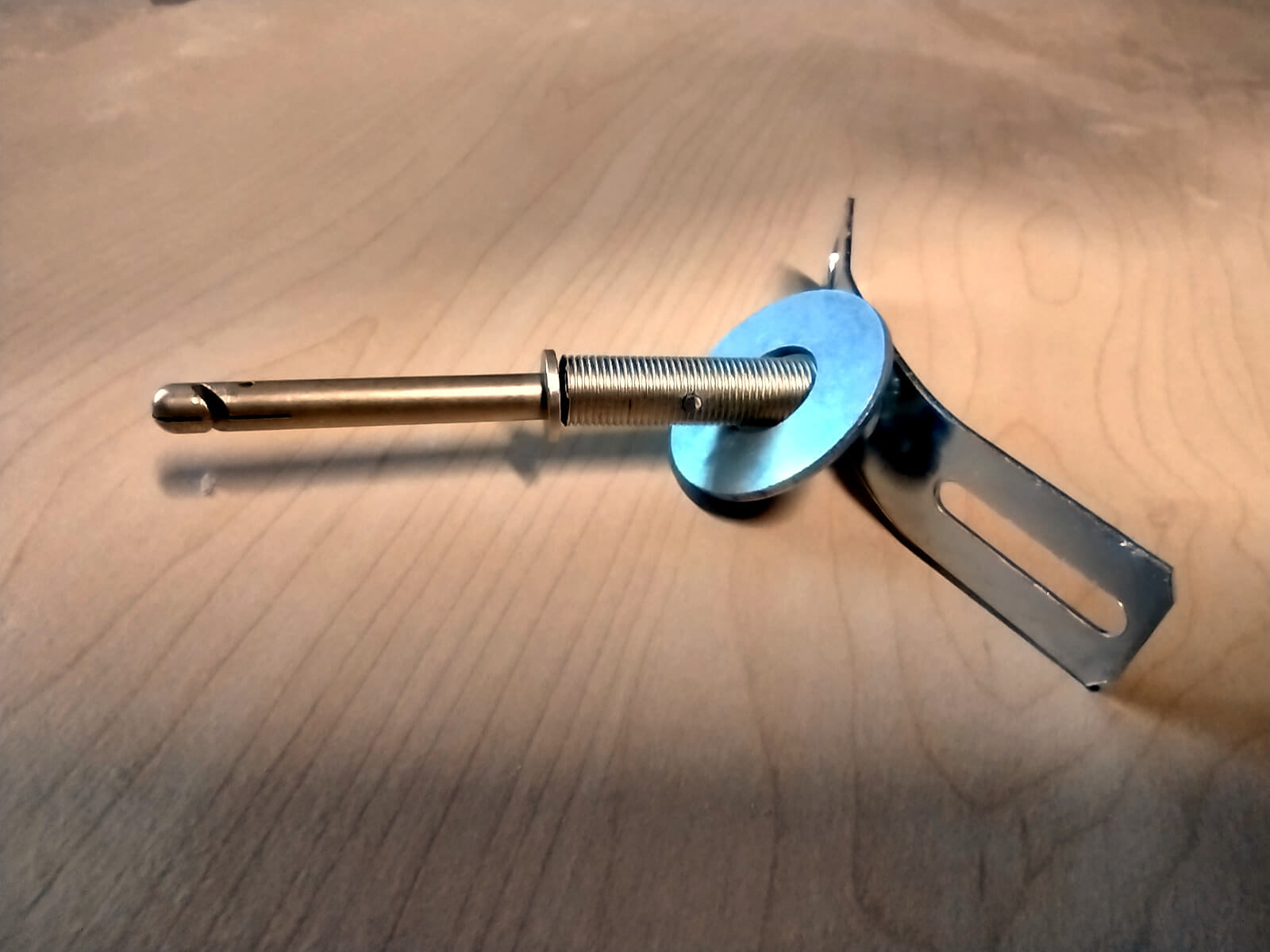
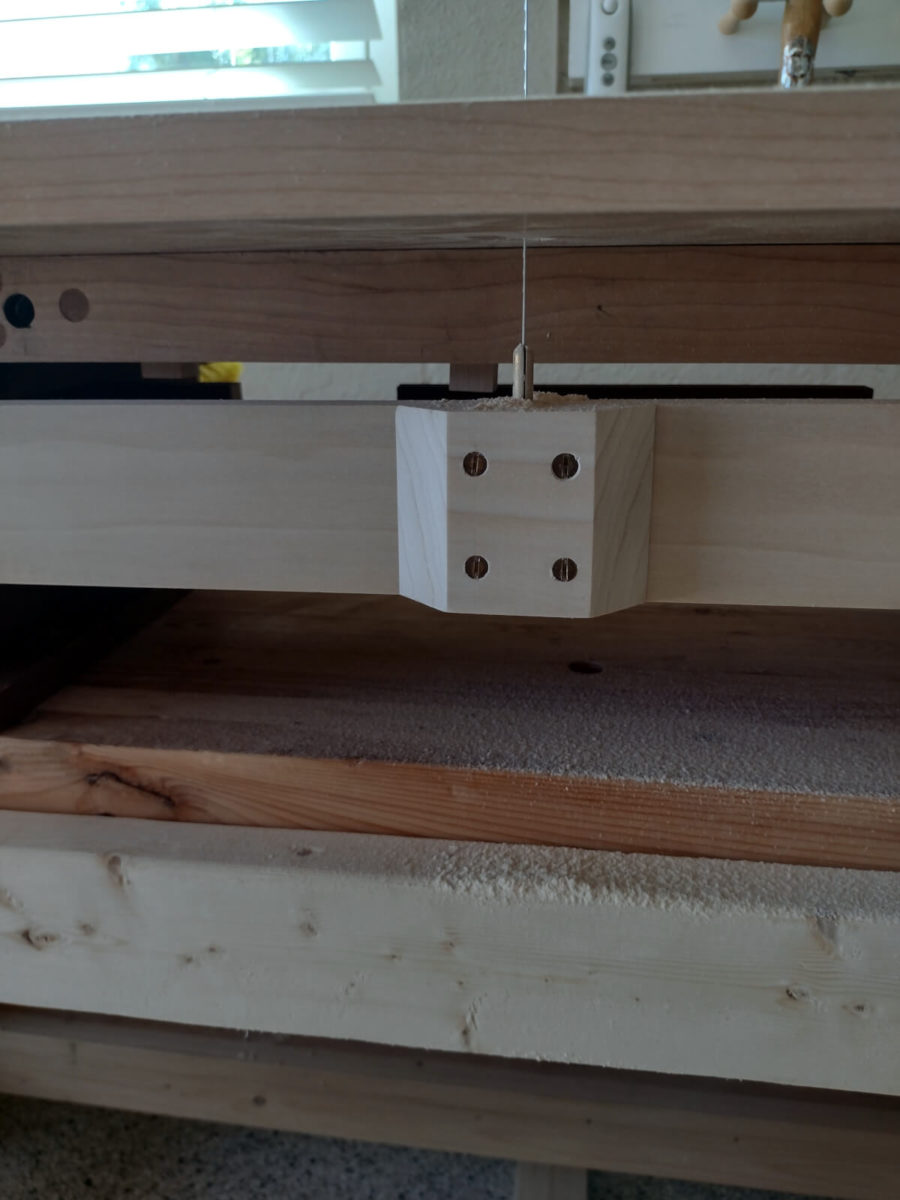
So, how well does it work? Two answers. The next photo shows the parts of a new carving project, all but one cut with this saw. They are 2 and 3 inches thick, with the longest being 21 inches long. The video shows a comparison between the old saw and the new.
What I haven’t shown you are the smiles that come along with using the new one.
Inspiration
The first inspiration appeared in the middle of a video made by Esteban Jiménez at his woodcarving shop in Barcelona. His treadle operated frame saw is gigantic in comparison to what I wanted. Impressive! Watch Esteban describe it and then demonstrate its operation:
Another inspiration is one of many examples I found of treadle operated fret saws used by marquetry artists. Here we see Christina Moreno using her frame saw: