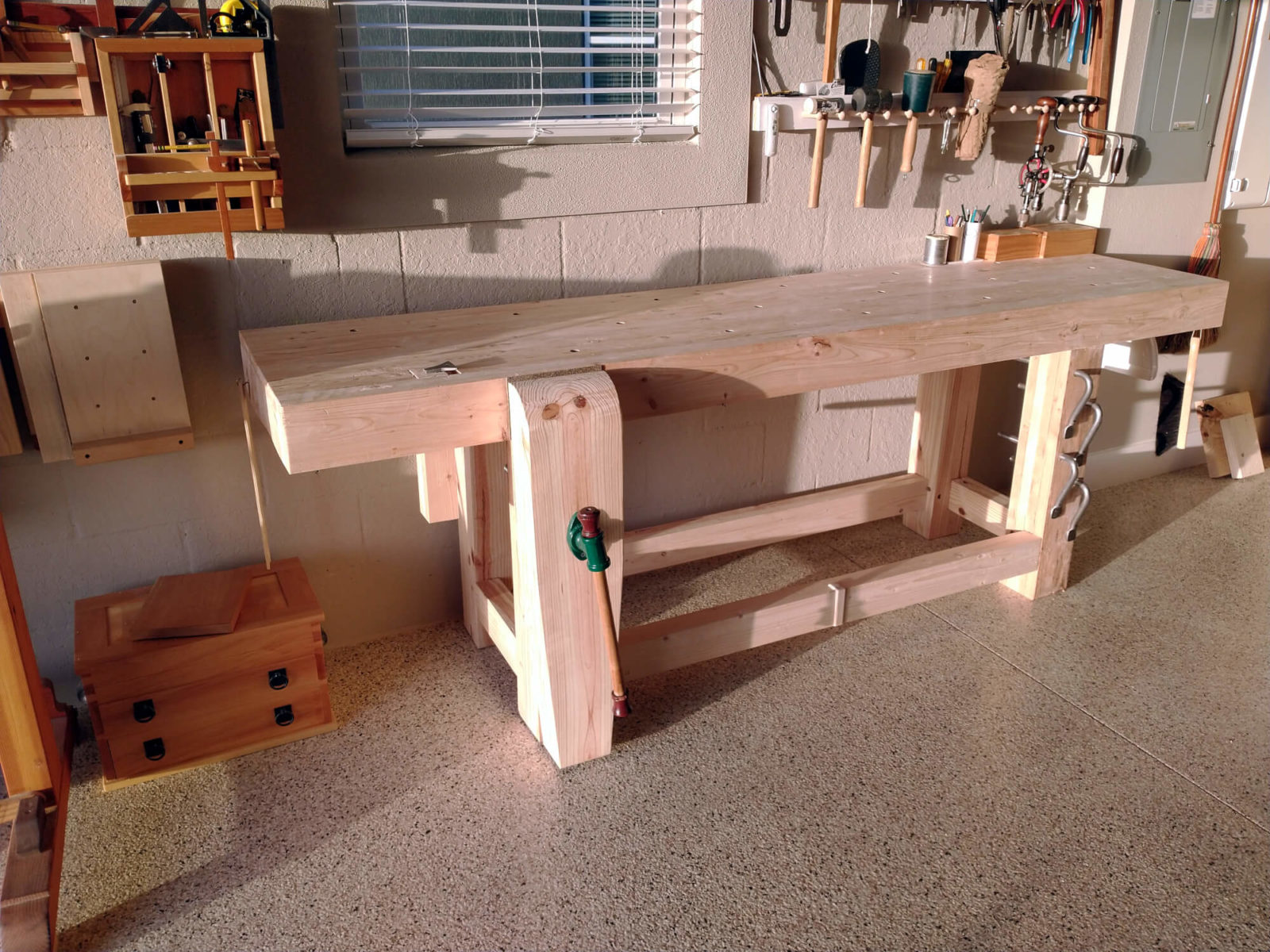
It’s been done for a couple of weeks and is already suffering HSS, Horizontal Surface Syndrome, the collecting of stuff on almost any horizontal surface.
- Design – Anarchist’s Workbench by Christopher Schwarz from Lost Art Press
- Dimensions – 100 inches long, 23 inches deep, 34 inches high
- Lumber – grade #2 Southern Yellow Pine from central Florida Lowes stores
- Vise – Crisscross from Benchcrafted
- Vise screw – 21 inch screw from Lee Valley Tools
- Vise accessory – Crubber non-slip cork/rubber from Benchcrafted
- Planing stop – Crucible Planing Stop from Lost Art Press
- Holdfasts – Gramercy Holdfasts from Tools For Working Wood
Note: I have no affiliation, nor collect any royalties, from any of these products. I simply enjoy their quality.