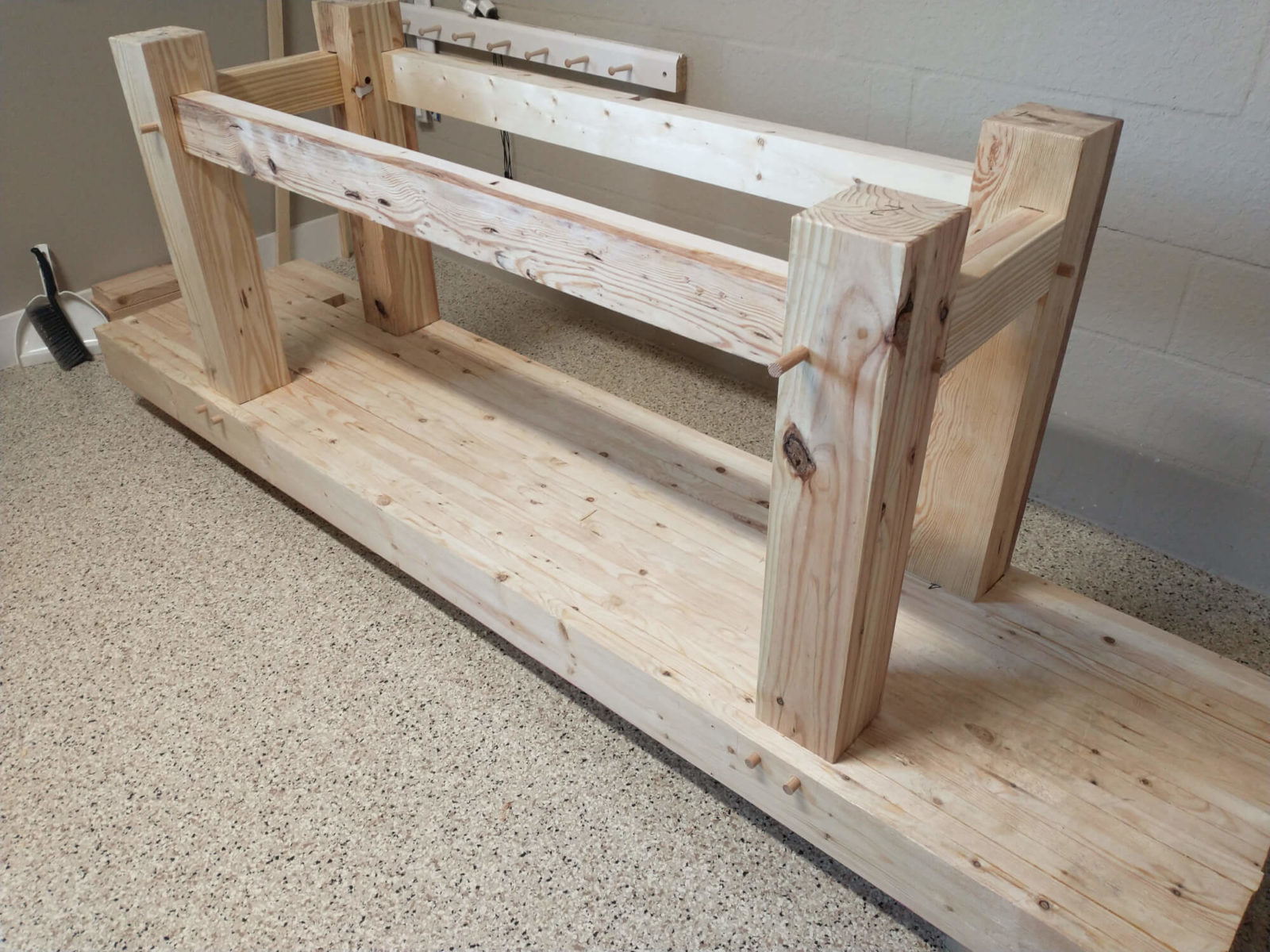
The Anarchist’s Workbench is ~mostly~ assembled, but it is upside down. How can I, myself, and me get it turned right side up? Yeah, I’m a hermit that won’t ask a team of strangers to throw their backs out. I’m also an enginerd with a simple understanding of physics. Here we see the bench resting on a couple of offcuts at each end, placed there to facilitate removing the clamps I used as levers for flipping the benchtop over. (See previous post.) Its time to engineer a way to flip the entire bench.
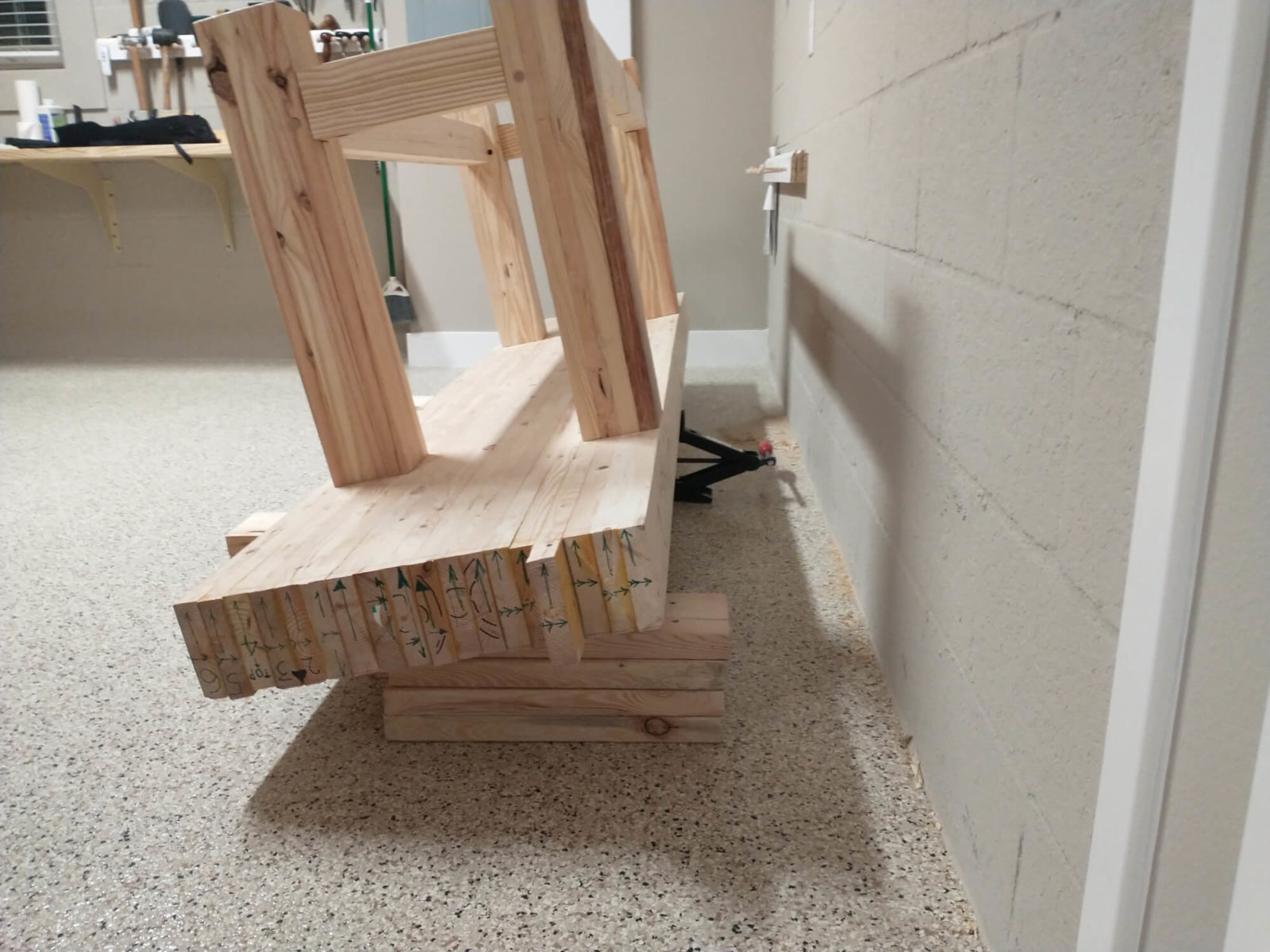
My F150 pickup truck has a great scissors jack that, fortunately, never gets used. Now is the time. First step, use it to tip the bench 90 degrees. Actually, I just moved it off center enough that tipping could be done with about 60 pounds of effort / control.
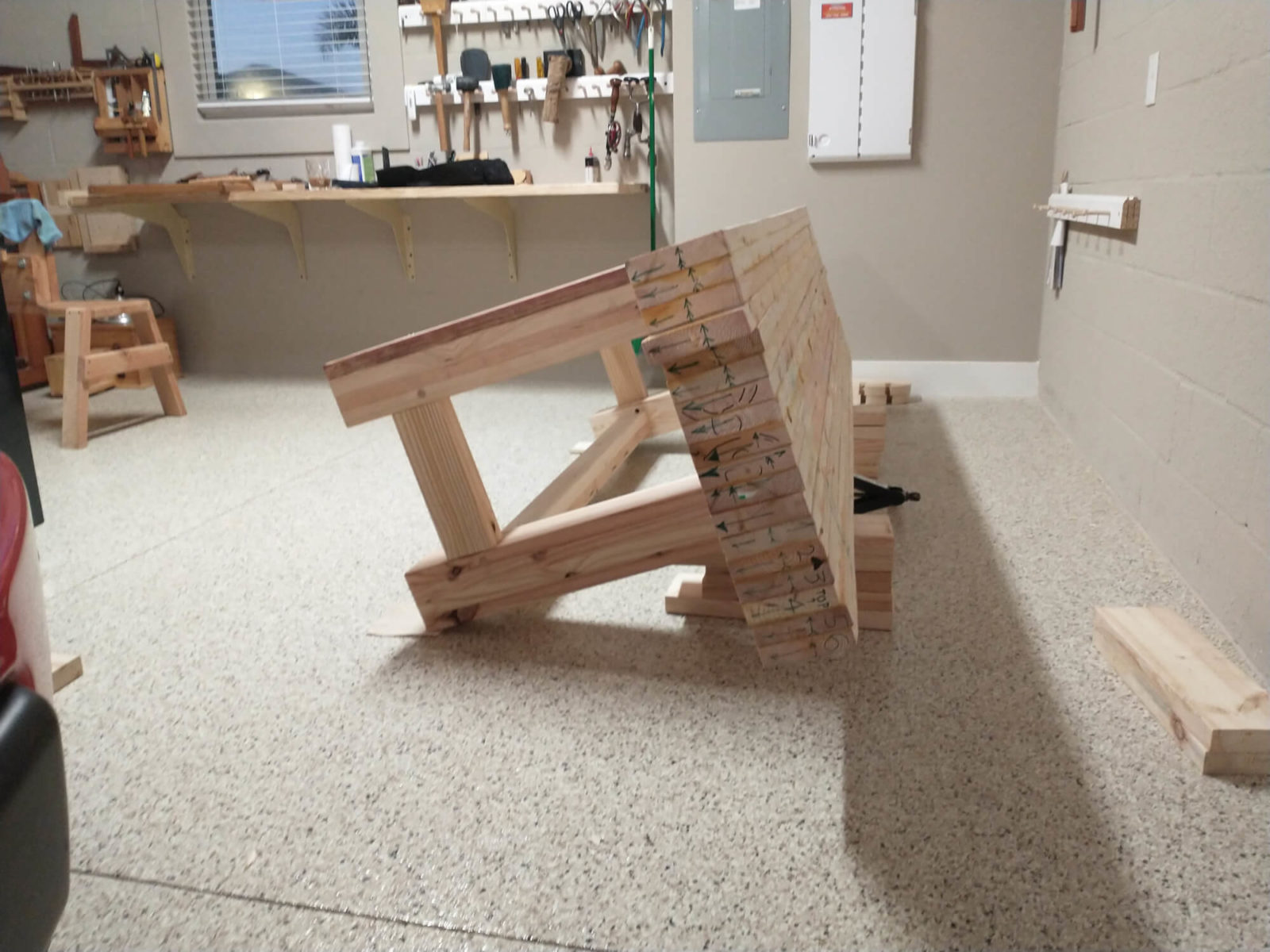
Start jacking up the back side. This is where the offcuts come in. I built two stacks of them while raising the bench. They serve two purposes, as a safety in case of sliding off the jack, and you’ll see the other purpose in the next paragraph. BTW, little patches of rubber shelf liner under the legs keeps the bench from sliding on the super smooth coated floor.
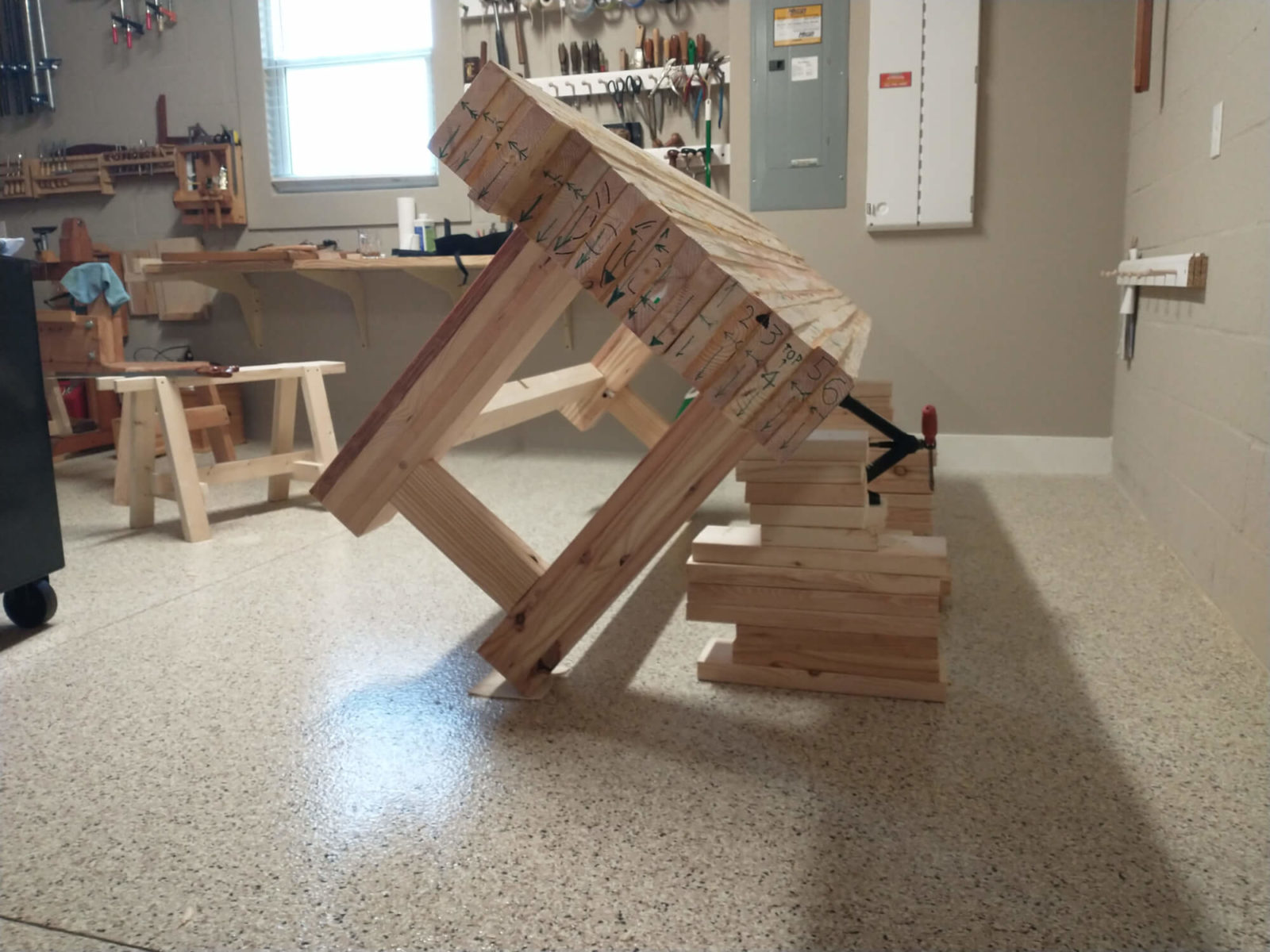
Keep on jacking. As the reach of the jack extends, let the bench rest on those stacks of offcuts and put a few offcuts under the jack to give it more reach.
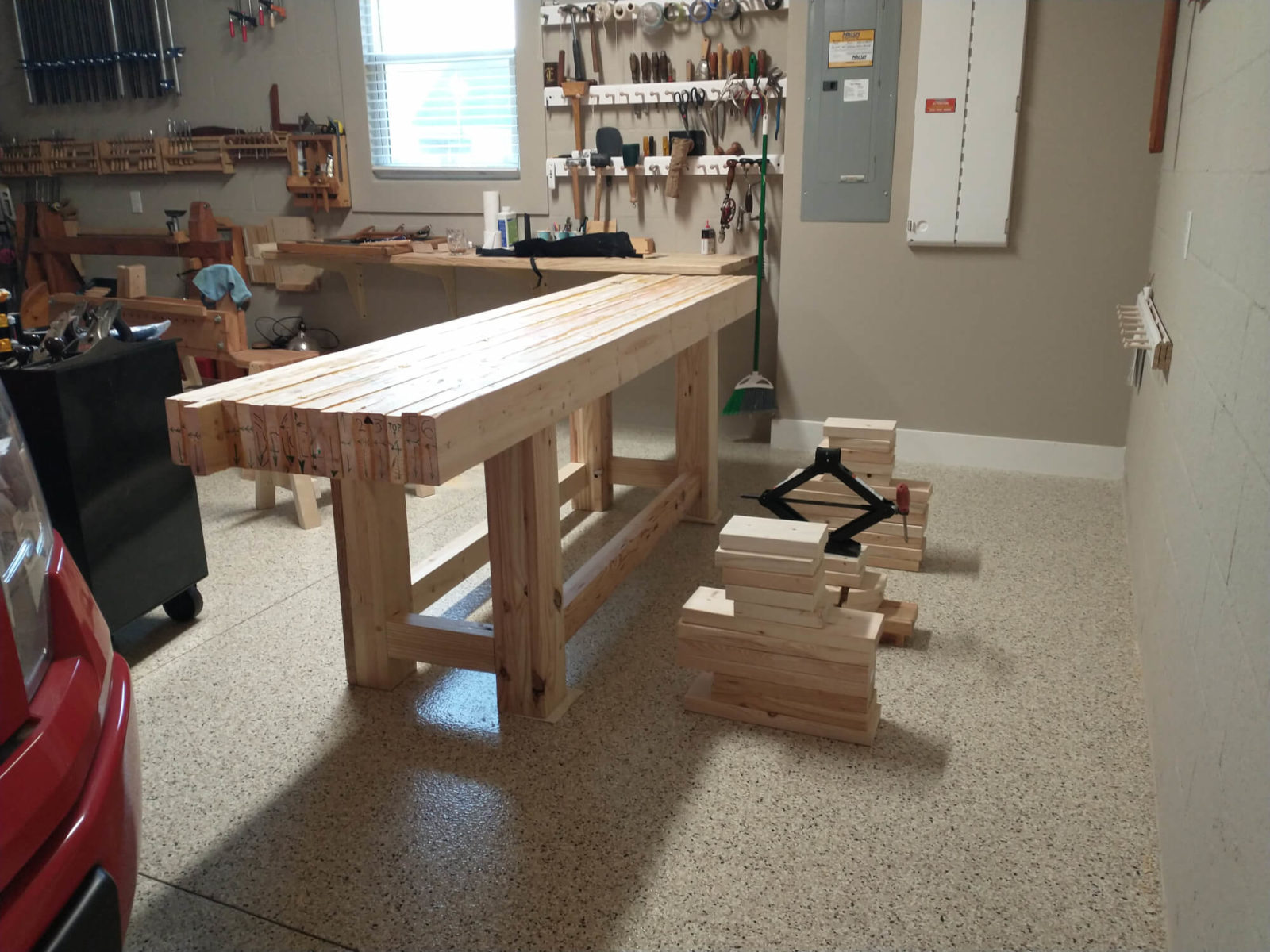
It didn’t need much more to reach another tipping point, where with only about 40 pounds of effort I tipped the bench over by hand and let it softly land upright.
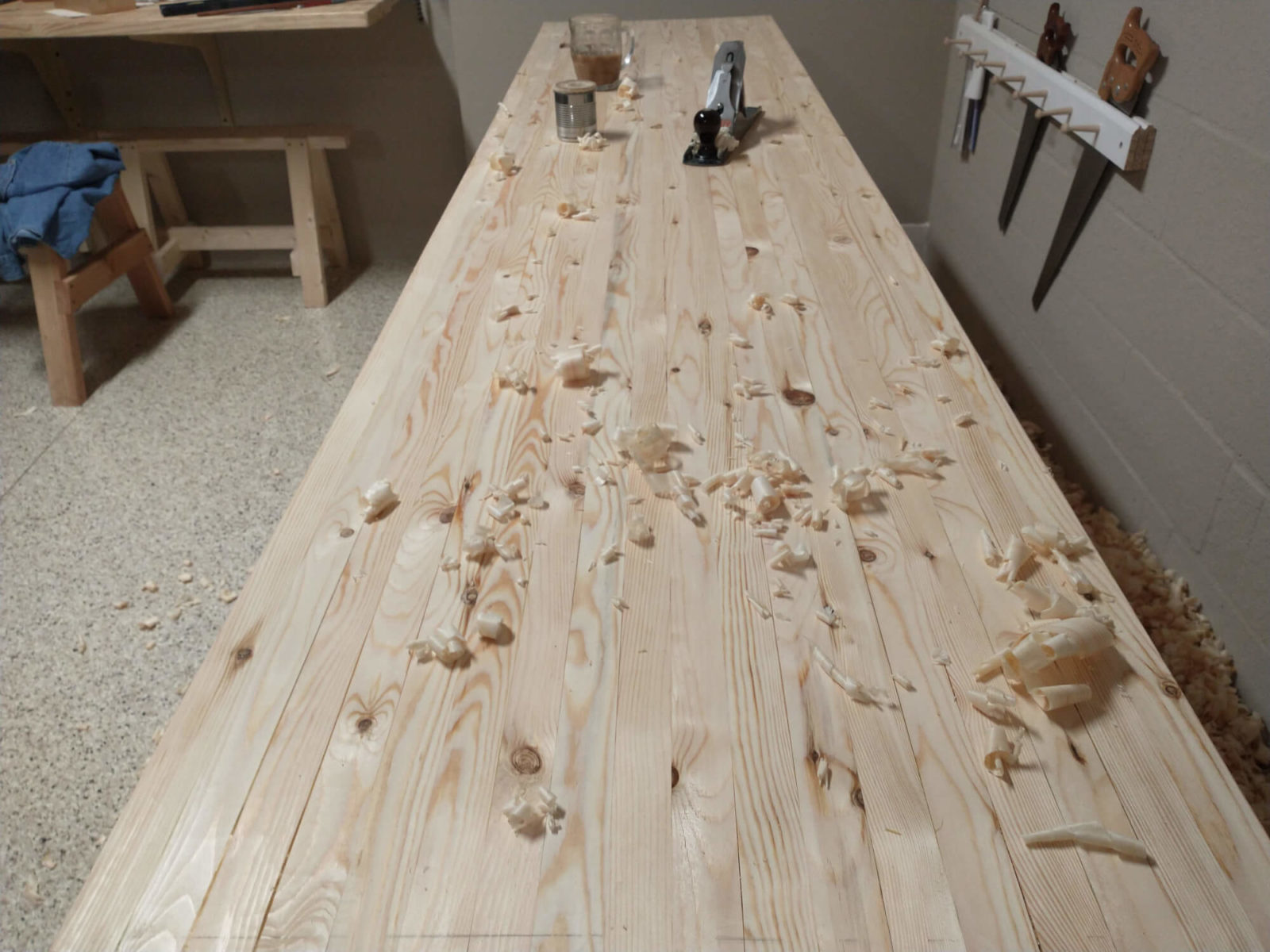
Call the donkey back for more planing. Here, flattening the top is partially done with a #5 scrub plane. Needs more….
Yet to be done:
- Finish flattening the top. (done)
- Saw off the ends. (done)
- Drill 16 holes for holdfasts. Schwarz has a pattern in the book. (done)
- Build a chop for the vise.
- Install the Benchcrafted Crisscross vise that I brought with me when we moved.