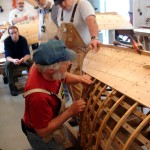
“Doc” Dan and I were hanging a plank on a Whitehall boat last spring. It was one of the planks at the turn of the bilge, a part of the boat with difficult curves in all directions. Dan and I had a beautifully spiled plank, a perfect fit. Yet, it took a good bit of clamping to keep it where it belonged while we screwed it down. When clamping a plank, it is very common to hear little cracks and squeaks as the plank rubs against any of the 24 frames of the boat. A much louder CRACK sounded as we tightened the 5th or 6th clamp. Dan and I stared at each other in wide eyed surprise. Then we examined the plank and found no cracks or splits. Our uninvited sound had come from a frame that cracked. It’s relatively easy to replace the plank (just a few hours of spiling and shaping), but much harder to replace a frame. Sigh! Our master shipwright, Greg, shook his had sadly and then gave instruction on how we could make a repair with epoxy.
The sinking feeling of an unexpected CRACK happened again with one of the Fiddlehead’s garboard planks. The last time I posted was after steaming the planks and temporarily fastening them. The next step was to remove them, apply an adhesive, and permanently fasten them. The stem of each plank was held by 4 screws. I set about removing all the temporary screws, not thinking much about the tension that might still be in the twisted wood. I removed them in the sequence shown in the picture (click the picture for a larger version). As screw #3 was removed, with #4 still attached, the plank cracked.
I sat in the moaning chair and diagnosed the failure as having two causes. The most obvious was removing the screws in the wrong sequence. The other was getting ahead in the sequence of things. The planks were originally left a couple inches long on each end. I trimmed off the excess after initial fitting. Had I left the excess, there would have been more meat around the screw holes and less probability of splitting.
The repair is a gap filling mix of epoxy and two additional screws. I think it is sufficient, but might add some additional patching on the inside later.
The white stuff is 3M 5200 adhesive. It is very much like construction adhesive, but is “Marine” grade which justifies at least tripling the price. It is very sticky stuff and gets all over everything. The stickiness lasts for days, as it takes 7 days to cure completely. It migrates so insidiously that some got onto a dog that was walking down the street, 50 yards away from the shop.