Nope, not a boat, but a very special project.
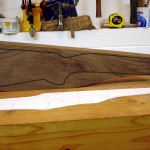
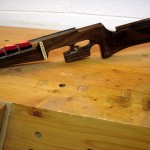
My daughter in law decided to ski a biathlon this coming winter, and started training some months ago. The biathlon is a combination of cross-country skiing and shooting, a fascinating competition. She will likely use an Anschütz 1827 target rifle, the gun that 95% of all biatleletes use. She wants a “dummy” gun to carry while training, and one that can also be customized to fit the way she wants to hold and use the gun. We decided to make a custom stock that could be modified as wanted.
Maybe there will be a more detailed post someday, showing some step-by-step work. For now, we have beginning and ending photos.