No power planer? Use a donkey.
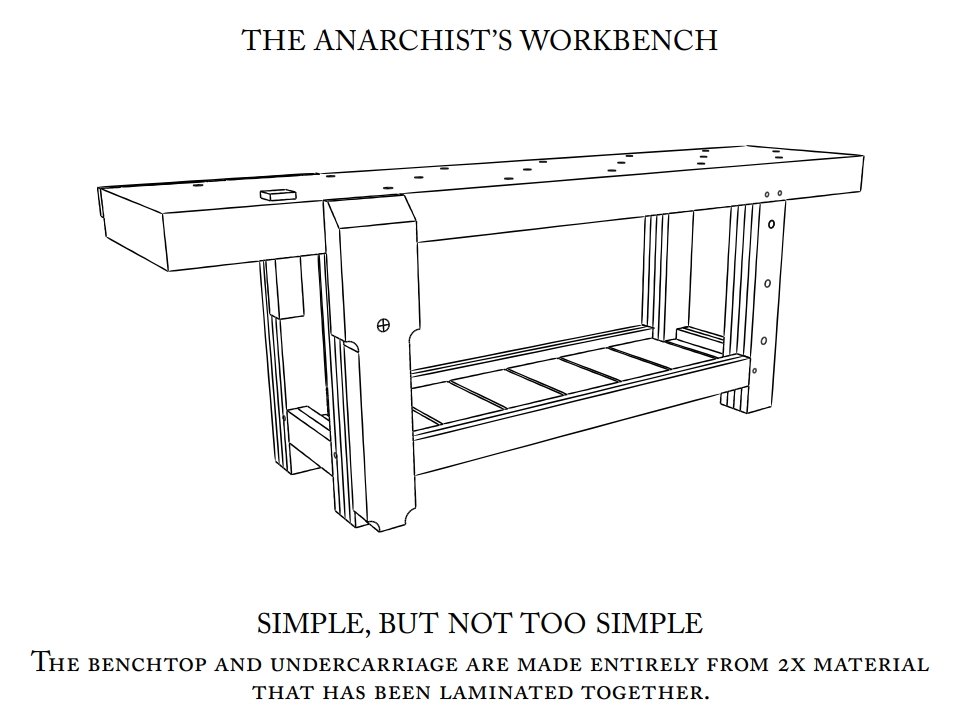
Schwarz describes building his Anarchist Workbench as mostly planing a bunch of boards and gluing them together. He emphasizes doing the planing and glue-up of any element (a leg, or a benchtop) in one day to avoid wood movement. That assumes a power planer. Well… I’m doing the job without a power planer, with only a couple of simple hand planes and a lot of “donkey work.” That makes me the donkey, and while it is tiring, it is also excellent aerobic exercise.
Schwarz also suggests using 2 x 12 lumber and ripping it into 2 sticks to make all of the 5 inch wide boards in this bench. I did that for the legs (16 sticks) and hated it. The best 2 x 12 lumber I can get here is #2 and not as nice as what Schwarz can find in his Kentucky / Ohio area. Our #2 Prime 2 x 12s have a very high resin content and knots as large as baseballs. OTOH, there’s an abundance of dry, straight, resin-free, 2 x 6 lumber with smallish knots. I’ve switched to 2 x 6 boards and find the donkey work much easier.
Colored chalk is for more than just sidewalks.
I arrived at a process by experience, and can now prep board for gluing fairly quickly. It goes like this…
- Cut to length. I’m wanting a finished 8 foot bench, but know I’ll have to trim the ends. So, I cut boards to 8.5 feet, 102 inches.
- Remove twist. There’s an important reason that Schwarz designated each board to be 1.25 inches thick, other than 4 x 1.25 equals an even 5 inches. After planing out the twist, there’s still enough thickness to get a 1.25 inch board from our standard construction lumber.
- Determine which face and which edge will be front and top respectively. Plan for glue-up to follow the grain patterns that always place the bark side of a board facing the heart side of its neighbor. Mark the ends of the boards appropriately. See this article for preferred gluing directions.
- Skim-plane one side of the board to ensure a flat surface for gluing. This is usually the heart side of the board, the side most likely to become convex.
- Mark the edges for 1.25 inch thickness.
- Plane a chamfer all around the edges down to the 1.25 inch mark and rub that chamfer with colored chalk.
- Reduce thickness (the real donkey work) with a scrub iron in a #5 Stanley plane. I do this by diagonally planing across the width of the board with a setting as coarse as I can push. See those spiral shavings. Keep going until the chalk mark is almost gone, about 1/32 of an inch.
- Change to lengthwise scrub planing to remove that last little bit of chalk mark and any noticeable high spots.
- Follow up with a straight iron and light setting to smooth out the scallops from the scrub plane.
- Next move to the top edge. Mark the board all around for 5.25 inch width.
- With the board standing on edge, plane the width down using a Stanley #78 plane. Start with 45 degree chamfers from each edge, then knock off the peak to bring the width down. With very coarse cuts it goes fast.
I don’t aim for exact width here, because gluing up always leaves slight unevenness and that can be dealt with when a whole unit is complete. If it ends up at 5 inches great. If a bit more, no big deal.
Workholding on a temporary bench
This temporary, bouncy, booming bench has no vice and no planing stop. I make do by creating a planing stop from a couple of boards that I have screwed to the bottom of the bench.
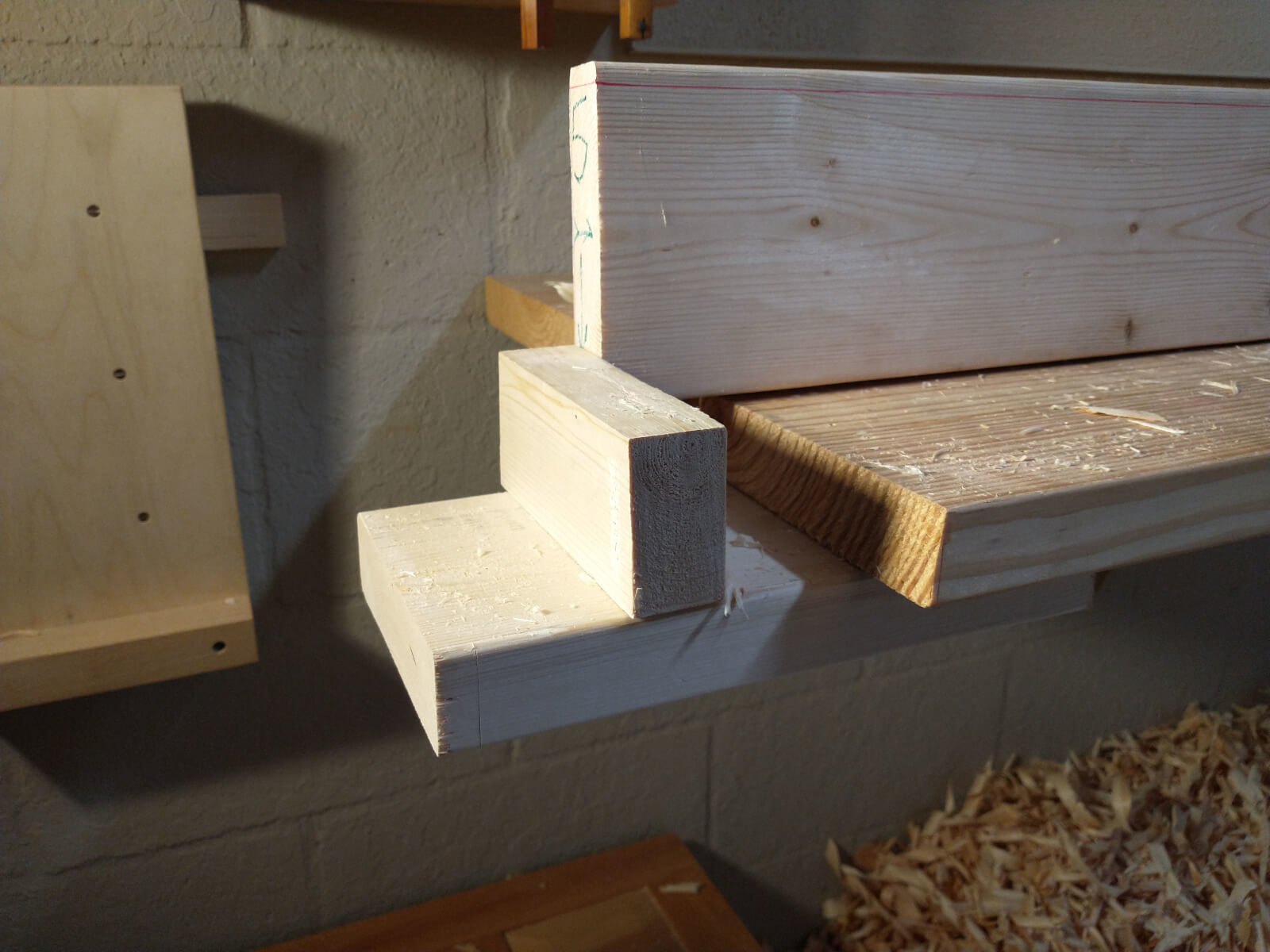
Likewise, a couple of 1 x 2 boards screwed to the top of the bench make anchor points for a variety of clamping solutions. Not nearly as fast and easy as holdfasts, but OK. Pic below is looking down.
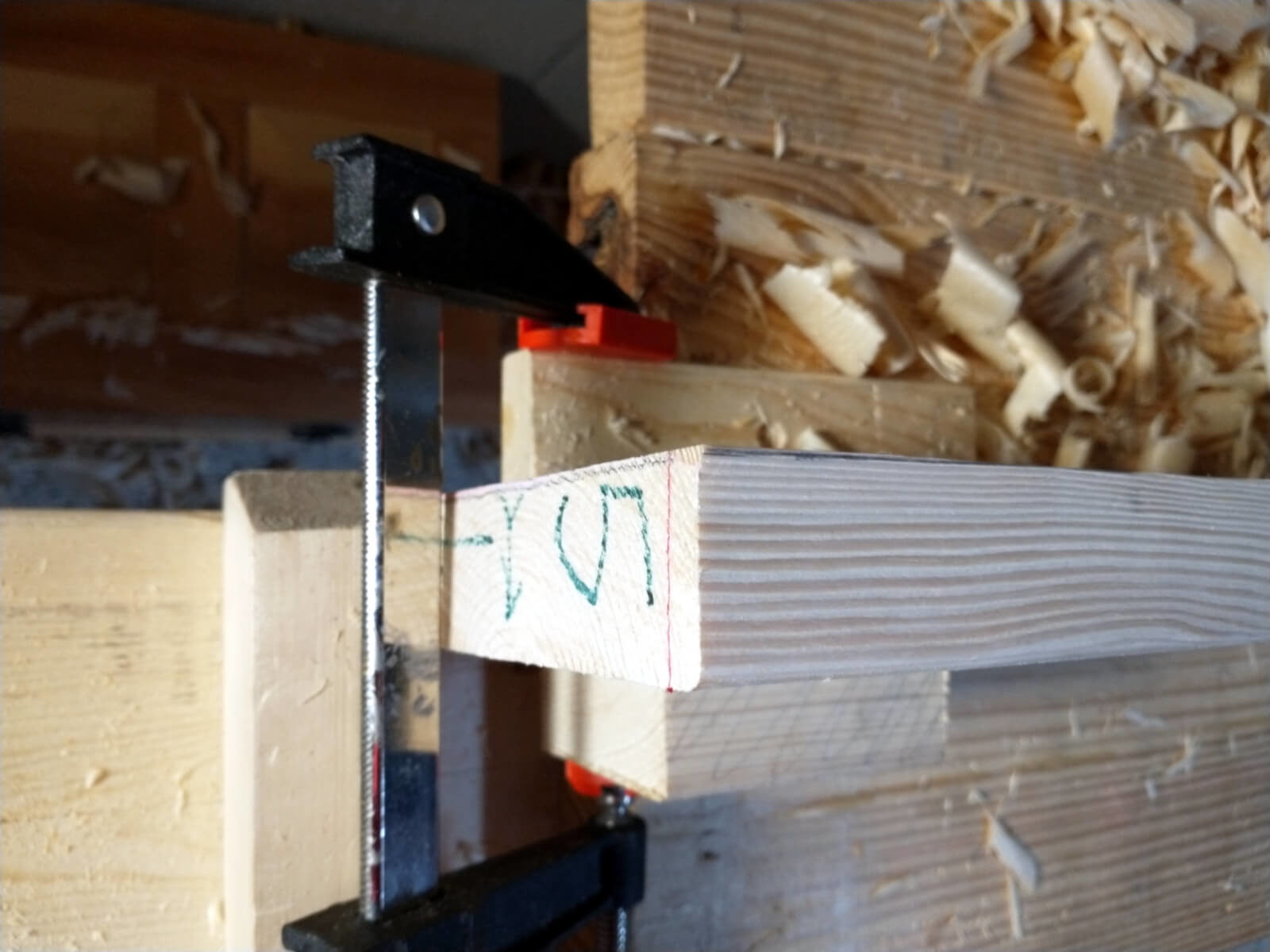
Yes, we have no bananas.
The first group of 6 boards worked out with none having any appreciable bow. BTW, there are 3 groups of 6 boards that make up the benchtop. As I started the 2nd group, the first two boards had a slight amount of bow, not too much to be corrected during glue-up … unless the 2 together established a result like a banana. How to keep them free of bow while the glue sets? My solution was to use another board at right angles (no glue!) to pressure the bowed boards into straightness. The other factor is using a bunch of iron pipe clamps.
Here, we see the edges of the two boards glued together and behind them the board laid at 90 degrees that keeps everything straight. (Note to self: add some tape to the edge of the straightener board to prevent it from being glued to the others.)
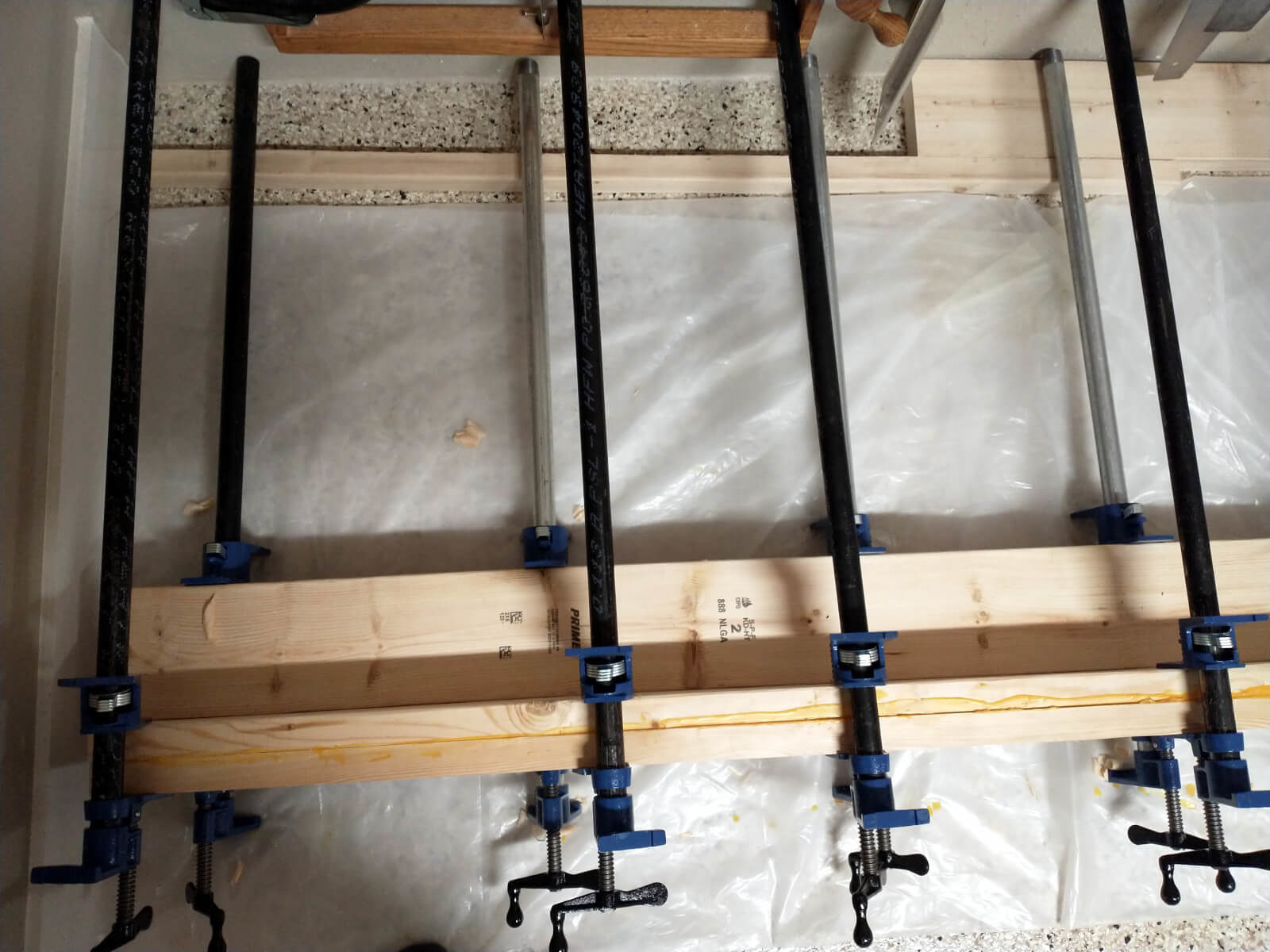
It worked. No bananas.
My daily gratitude is for being blessed with good health, having a very short (20 seconds) commute to my workshop, and having plenty of time to spend with Eva. This 77 year old donkey is staying very active and is now only 8 boards away from completing the bench top.