Effective immediately, my PayPal account is closed, and my eBooks are no longer available.
First, PayPal:
Someone, or maybe many someones, at PayPal have chosen to climb aboard the woke train. They, like many other social platforms and some corporations have decided that if you don’t accord their beliefs they will fine you or cancel you, or both. PayPal has been rather quietly deplatforming, erm “suspending”, their customers for some time, but last week updated their Acceptable Use Policy to be able to fine people (steal from their account balances) up to $2500 for sins of offering unacceptable discourse.
Oh! They “never intended” to release that notice:
“An AUP notice recently went out in error that included incorrect information,” the spokesperson said. “PayPal is not fining people for misinformation and this language was never intended to be inserted in our policy.”
Yes, they have recanted that news, but have actually left enough of the policy in place to use it when they want.
These policies are blatant censorship, assaults on free speech. I’ll have none of it. My account is closed and I say “Good Riddance” to the woke idiots who want to ruin their own business.
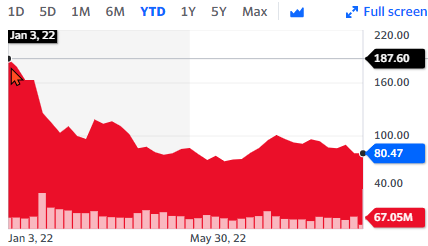
REF: https://reclaimthenet.org/paypal-fine-2500-intolerance-discriminatory/
REF: https://reclaimthenet.org/how-to-delete-paypal/
UPDATE:
A follower very kindly contacted me within minutes of publication of an article about alternatives to PayPal. Sincere thanks for that pointer! Maybe it can also help those of you who also operate online businesses. Read: 10 PayPal alternatives – for privacy or free speech
Second, my eBooks:
MANY THANKS to those of you who over the years have purchased my eBooks. As you might know, those were simply collections of my own articles on particular topics. Pulling them together into single documents was done for reader convenience. Sales have done well enough for such a minor adventure. They were interesting to assemble and have apparently been useful to many of my readers. I sincerely appreciate all who bought them. Thank You!
Alternatives? Today’s wokeness with payment processors is something I can no longer tolerate. PayPal’s deplatforming is well known and the next most popular alternative, Stripe, has also shown a woke stripe. As did the third choice, Amazon. We can keep walking down the list of other payment processors and find more of the same. I don’t have the energy to continue looking for others. I’m done.
P.S. Long time readers know that this blog is for hobby interests. While I have strong political views, I don’t express them on this blog. I have no Twitter account. My Facebook account was suspended years before the pandemic for a reason I don’t even remember. The only other social media account I have is an Instagram account where I post nothing and keep the account only to observe other artisans. So, it’s not like I’m a rabble rouser, I am simply a strict First Amendment believer.
“Liberty is meaningless where the right to utter one’s thoughts and opinions has ceased to exist.”
– Frederick Douglass